Our Process
Our process is simple. We establish a full understanding of what our client wants – their expectations, requirements, constraints. Then we work out how to deliver it. Frictionless coordination and management of supply chains is a unique strength of ours. We have a proven track record in delivering complex projects with a wide range of trade interfaces.
Scoping, Tendering & Brief Definition
We are familiar with a broad range of approaches to commissioning our products and services and are adaptable to various procurement routes. Our estimating and pre-contracts team will work with you and review the available documents to understand the project scope and parameters. From the outset, we aim to provide clear communication, high quality quotations and proposals and an outstanding service. Where appropriate, we are also happy to provide early engagement services and cost planning advice on concept design information.
01
Design Development
Soon after appointment, we allocate a design team who work closely with the project team, attending workshops and creating shop drawings. We incorporate the details of joinery construction and specialist finishes into our initial proposals to ensure the finer details are captured and any issues are overcome before we release for manufacture. Samples and mock-ups are produced for approval; and during this process we like to engage our supply chain to ensure we capture their requirements and identify potential limitations with the proposed materials early on. The team coordinate design information carefully, sharing details with architects and main contractors so the joinery can be manufactured and installed with the upmost precision and efficiency, while accounting for time and cost considerations.
02
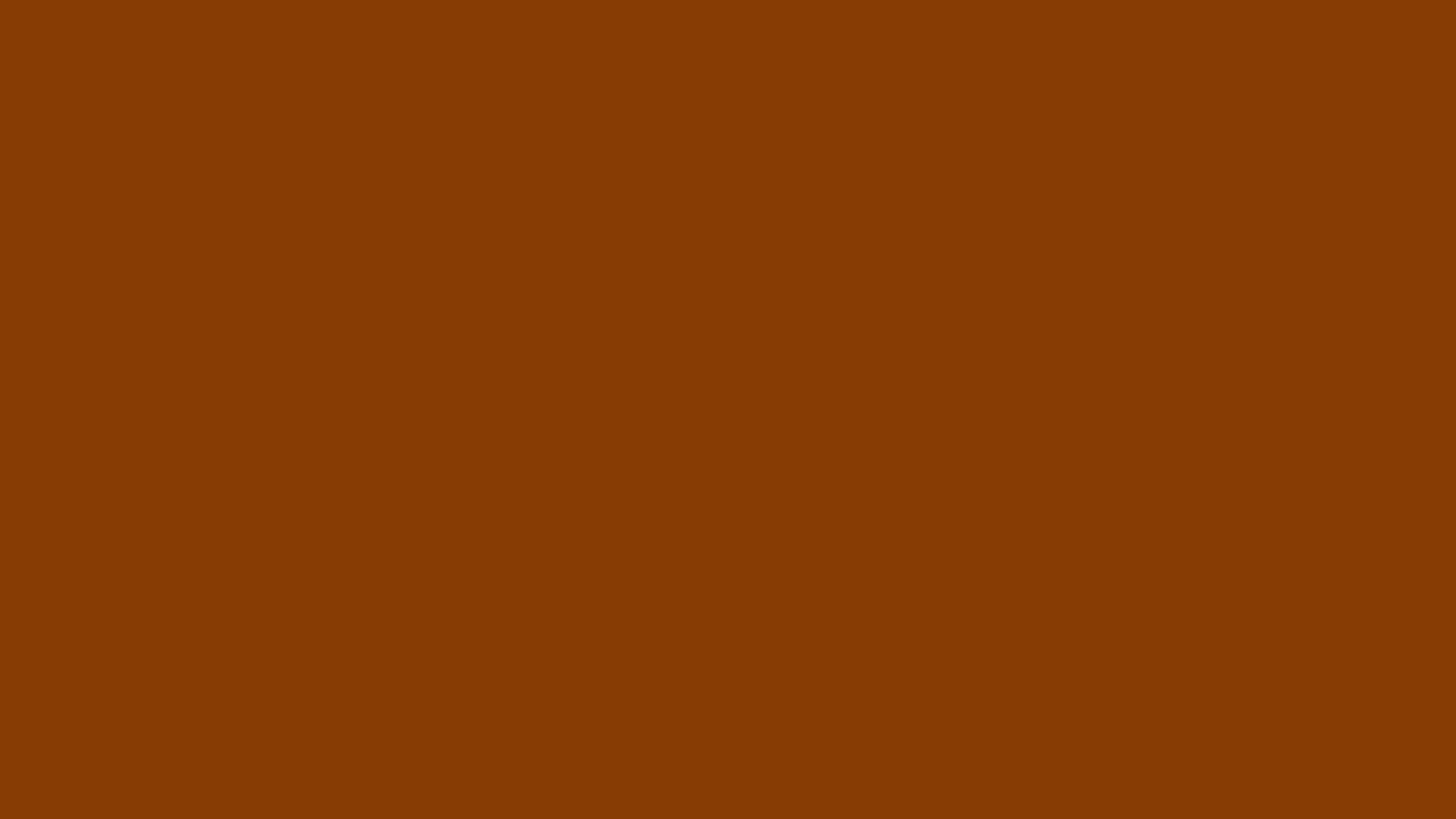
Manufacturing & Production
With over 28,000 sq/ft of production space including 4,000 sq/ft of storage on our premises, we offer a high level of scope and flexibility in manufacturing. Two Computer Numerical Control (CNC) machines with 5-axis cutting allow us to machine extremely complex configurations to the greatest accuracy, cutting lead-in times, increasing efficiency and reducing waste. We also have four state-of-the-art spray booths and in-house veneering capabilities. Quality checks are carried out at every stage as an item of joinery progresses through the departments. All joinery undergoes a further internal review prior to dispatch.
03
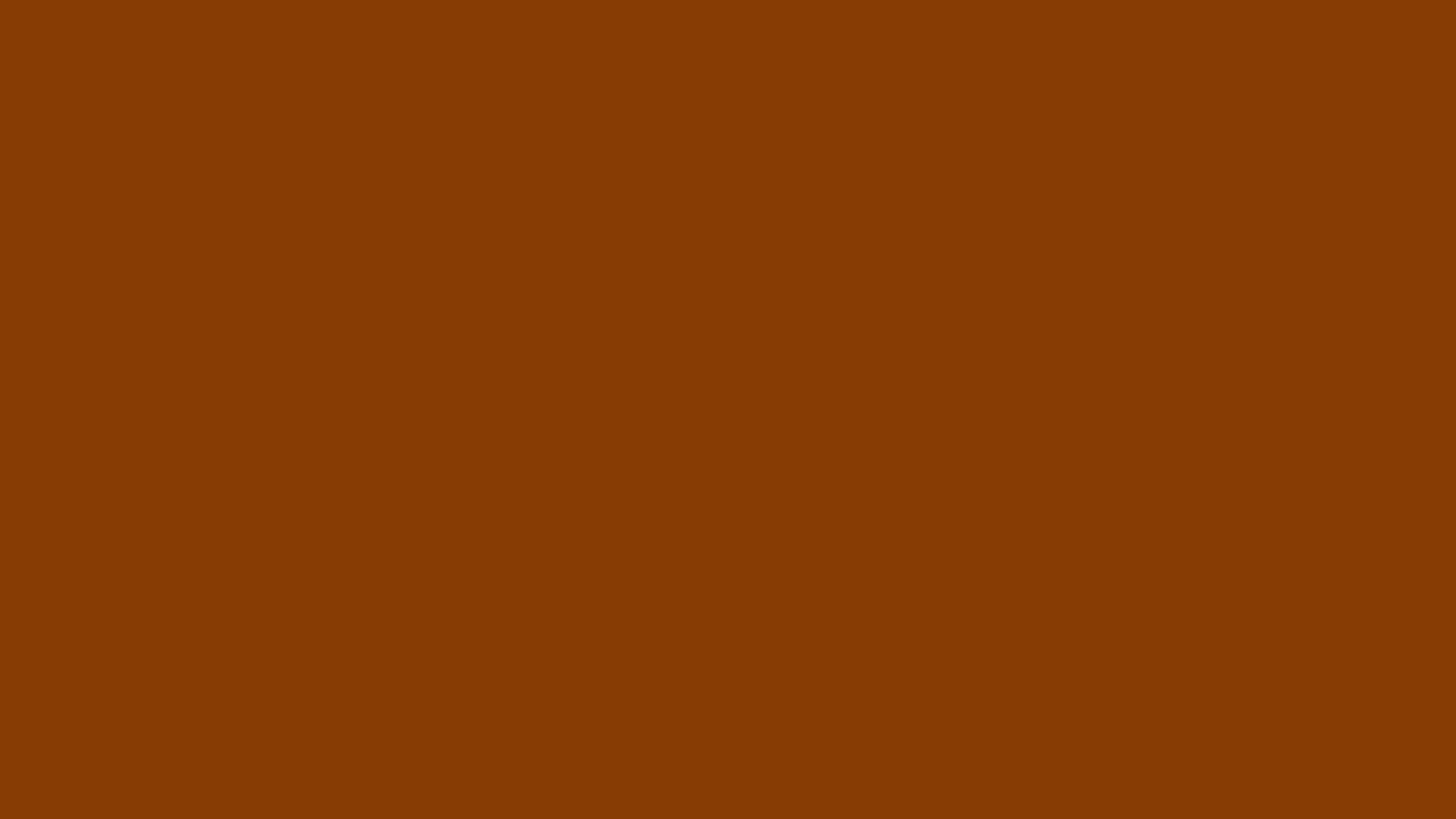
Install & Fit-out
We employ 22 people in our installation team, all highly skilled and engaged professionals who work alongside other tradespeople with consideration and respect. Every project is allocated an installation manager, who works closely with clients and is present onsite during concentrated periods of installation work. And quality control is constant; we complete a thorough internal review in addition to any additional client processes prior to seeking sign-off. As key players in the closing out of projects, we recognise that our joinery is often integrated with the overall completion – and ultimate success – of a project. We are therefore keenly aware of the need to complete it as planned and on time, coordinating closely with other trades.
04
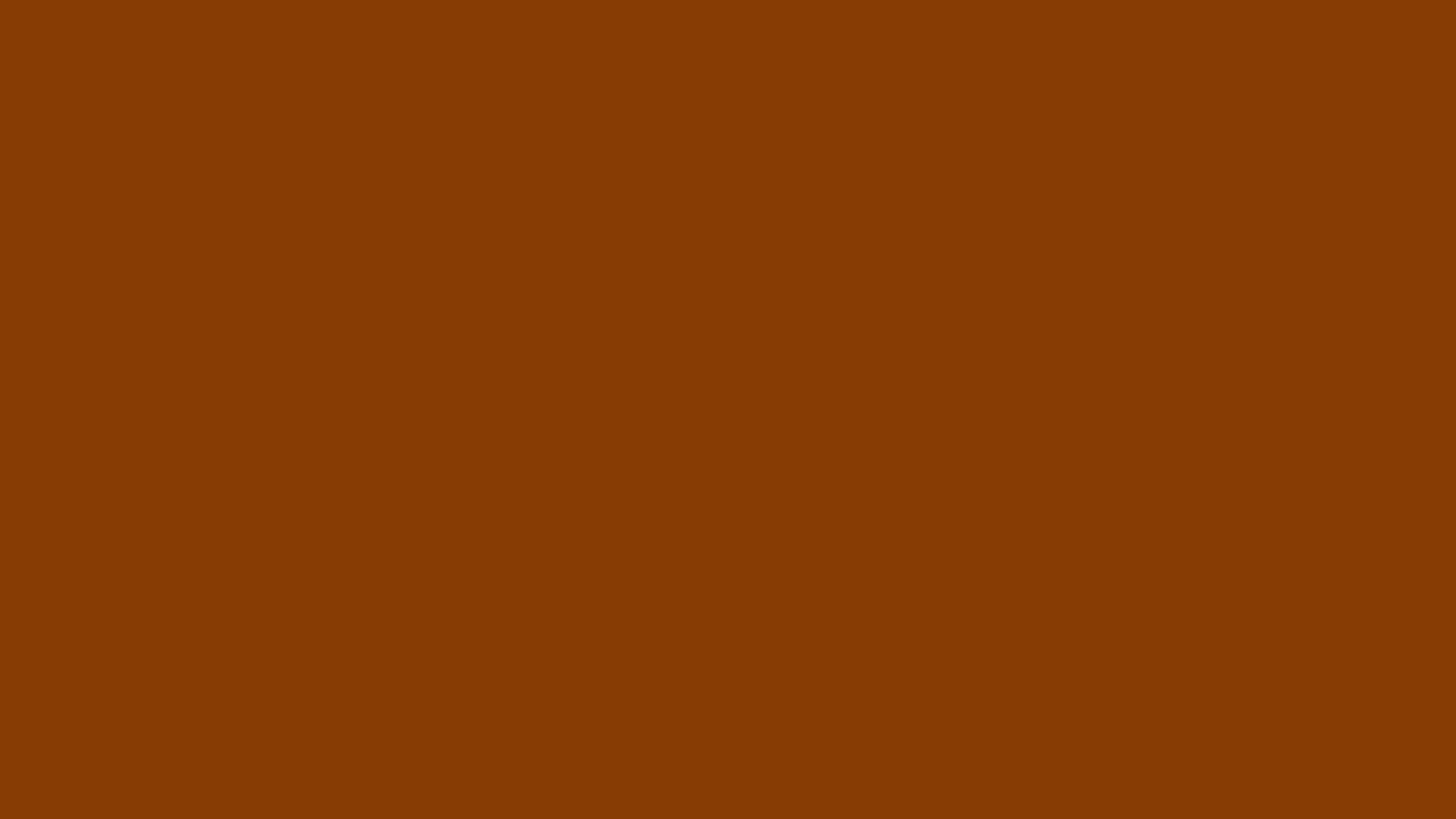
Aftercare
For UK-based projects, we can provide planned and reactive maintenance services. This might include repairs or touch-ups for general wear and tear, additional works or changes to the installed joinery. We can also provide preventative maintenance, such as the adjustment and/or of mechanisms, fittings and hardware. Aftercare support is provided from our London office, where we can arrange site visits as necessary.
05
“NBJ performed well throughout the drawing design stage, project management, production and installation, demonstrating strong leadership skills and organisation. NBJ’s eye for detail and finish ensured that the vision for a new library was fulfilled.”
– Tom Wakeford, Joint Managing Director
Stepnell